Best Practices for Maintaining Your Impregnation Line for Longevity
- Ambica Impreg
- Dec 25, 2024
- 4 min read
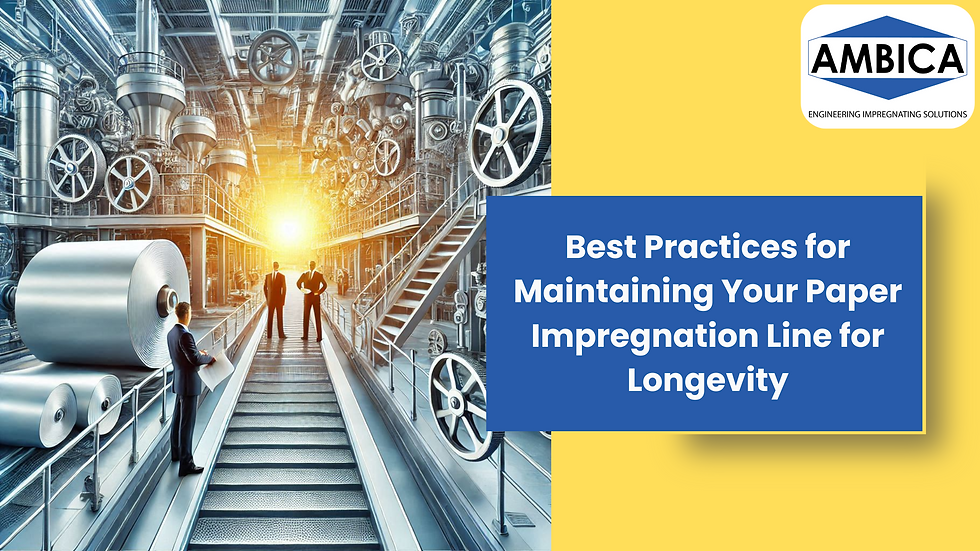
Maintaining the longevity and efficiency of your paper impregnation line is essential for ensuring optimal production and reducing the risk of downtime. Proper care and upkeep not only enhance performance but also contribute to the consistent quality of products, reduce maintenance costs, and extend the life of critical components. In this blog, we explore the best practices for keeping your impregnation system running smoothly, ensuring long-term reliability and productivity.
1. Regular Inspection and Preventive Maintenance
Routine inspections and preventive maintenance are essential for maintaining the efficiency of your production system. Regularly checking critical components such as tanks, curing chambers, rollers, and pumps helps detect potential issues early. Addressing minor problems before they become major can avoid expensive repairs and unplanned downtime.
Focus on inspecting the following:
Tanks and Chambers: Ensure they are free from blockages or residue buildup.
Rollers and Pumps: Check for damage or wear that could impact fluid transfer or product uniformity.
Heating Systems: Ensure proper temperature regulation to avoid inconsistent curing.
Adhering to a maintenance schedule that includes these routine checks will help preserve the equipment's performance.
2. Effective Cleaning Practices
Keeping the system free of contaminants is crucial for maintaining quality and avoiding breakdowns. Regular cleaning of tanks, pipes, and other components prevents the accumulation of resins, adhesives, or other materials that could compromise the process. Depending on the substances you work with, residues can build up over time, causing blockages or inconsistent processing.
To maintain the effectiveness of your system, follow these cleaning steps:
Chemical Solutions: Regularly flush the system to avoid the accumulation of chemicals that can alter mixtures.
Mechanical Parts: Clean rollers, filters, and nozzles to ensure they remain free of debris.
Fluid Circulation: Check pumps and fluid paths for contamination, as this can affect the chemical application.
By ensuring consistent cleaning practices, you avoid performance issues related to residue buildup or contamination.
3. Maintain Optimal Chemical Mixtures In any impregnation process, the correct balance of chemicals is essential to achieve the desired quality. Changes in chemical concentrations over time can lead to inconsistent results and may require adjustments to the formulation. Monitoring and maintaining the right chemical mix for each batch will ensure uniform application and reduce the risk of waste or product defects.
Regularly check and adjust:
Chemical Concentration: Use measurement tools to ensure the proportions match the desired mix.
Mixing Equipment: Clean mixing tanks and pipes regularly to prevent chemical residue buildup, which could skew the mixture.
By focusing on the consistency of chemical application, you can achieve uniform results throughout the process.
4. Hydraulic and Lubrication System Care Proper lubrication is critical for reducing friction in moving parts and extending the operational life of machinery. Follow manufacturer guidelines regarding lubrication schedules and types of lubricants to ensure the system runs smoothly. In addition, maintain the hydraulic systems, checking for leaks or other issues that could cause disruptions.
Key areas to focus on include:
Lubricating Components: Keep gears, motors, and moving parts well-lubricated to minimize wear.
Hydraulic Systems: Ensure that pumps, valves, and hoses are properly maintained to avoid leaks and performance degradation.
With a well-maintained hydraulic system, your production process will run efficiently and with minimal disruptions.
5. Temperature and Humidity Control Both temperature and humidity play a significant role in the impregnation process. Fluctuations in these conditions can lead to inconsistencies in the product and cause inefficiencies in the curing process. Implementing temperature and humidity controls can help regulate the atmosphere and maintain consistent quality.
Monitor and adjust:
Temperature Sensors: Ensure accurate readings to maintain the correct environment for curing.
Humidity Levels: Control the moisture levels within the system to prevent improper chemical reactions or drying issues.
Consistent environmental conditions help maintain the performance of your impregnation system, ensuring optimal operation over time.
6. Staff Training and Awareness The operation of any complex machinery, such as a paper treatment system, demands skilled operators who are well-versed in the maintenance needs of the equipment. Regular training for staff on best practices for operation and maintenance ensures that the system is used efficiently and problems are detected early. Additionally, well-trained teams can prevent mishandling or accidents that could lead to costly repairs.
Training topics should include:
Routine Checks: Teach employees how to perform regular inspections and identify potential issues.
Maintenance Protocols: Ensure that staff members are familiar with cleaning schedules, lubrication, and troubleshooting.
A knowledgeable team contributes to smoother operations and better care for the equipment.
7. Control Flow Rates The flow rate of both the chemical mixture and the material being processed is crucial for consistency. Excessive or insufficient flow can result in uneven application or a waste of resources. Regularly monitor the flow rates to maintain proper consistency in the impregnation process.
Ensure that:
Flow Meters: Regularly check meters for accuracy.
Adjustments: Make necessary adjustments if flow rates deviate from the set values.
Maintaining consistent flow is essential for the efficiency and product quality of your impregnation process.
8. Use High-Quality Spare Parts
To ensure that the system continues to function at its best, use only high-quality replacement parts when repairs or replacements are necessary. While it may be tempting to opt for cheaper alternatives, low-quality parts can lead to system malfunctions or inefficiency.
Invest in:
OEM Parts: Use original equipment manufacturer parts designed for your system.
Durability: Choose parts that can withstand the wear and tear of continuous operation.
By choosing high-quality components, you can reduce the chances of early malfunctions and extend the lifespan of your system.
Conclusion
Proper maintenance is vital for extending the life and efficiency of your paper impregnation line. By following the best practices outlined above such as regular inspections, effective cleaning, consistent chemical monitoring, and proper staff training you can enhance the performance, quality, and longevity of your equipment. Implementing these practices will ensure that your system runs smoothly, ultimately contributing to higher productivity and reduced downtime.